
My son Bradley’s 1982 Chevrolet Corvette continues to create its own adventures.
He spent a weekend at Sauer’s Machine and Racing, a shop in Medford, OR. His grandfather, Dick Ewing, who dragged-raced a C1 Corvette and was known for his ability to work wizardry with nitrous injection, works as a technician there. Bradley drove himself there and back in the Shark, a roundtrip of nearly 600 miles.
With his grandfather supervising, he spent two days going over the car. He replaced the distributor cap and rotor, along with the oil pressure sending unit, as the original had failed. He did the work himself.
The car had a stiff ride. They discovered that the cheapie Chinese-made aftermarket shocks had failed and were permanently collapsed. They put KYBs on the front and Monroes on the back.
He had just started the drive home in 90-degree weather when he realized that although he could hear the fan blowing, there was no cold air coming into the cockpit.
After a quick call to his tech in Portland, Chip Starr, he returned to the shop. Chip noted that there is vacuum line that opens the flaps that lets cold air into the cockpit, and it might have gotten dislodged while they were replacing the distributor cap.
In fact, that was the case. Bradley quickly located the disconnected line, reconnected it and had an uneventful trip home, cold air blowing.
Along the way, he heard a rattling noise from the front and suspected it had something to do with a shock.
The next day he took the car to the SCM Batcave, where we store the 1967 Alfa Romeo Duetto, 1965 Giulia Spider Veloce and 2006 Lotus Elise. (The 1975 Porsche 911S is about to join the group, but that’s a story for another time.)
Bradley had never gone to our off-site garage by himself, nor ever used any of the tools. He called me, amazed. “You have a roll-around tool chest here! And a floor jack. And a big compressor.” Indeed.
Using a 9/16” box end wrench, he reached past a front tire and tightened up a loose nut on the shock and was on his way.
My grandfather, who raised me, died when I was 11. I inherited his small chest of Craftsman tools. They were what I used while learning to work on cars. I had no adult to guide me and relied on fellow car owners and club members.
I confess to a warm feeling knowing that my son is touching and using the very same sockets, ratchets and open- and box-end wrenches my grandfather did over half-a-century ago.
This analog Corvette continues to be the giver of lessons. Bradley was immensely proud of his ability to change out the shock absorbers and improve the handling of his car. He also was pleased that he was able to locate the disconnected vacuum line, reconnect it and get the A/C back.
We live in a digital world where opportunities to be able to touch and repair things are increasingly infrequent.
The mantra to making any old car reliable is “drive, break, fix, drive, break again, fix again and repeat as necessary.”
The Corvette is more than 40 years old and has covered 95,000 miles. It has not been in regular use for over a decade. This process of making it a reliable, trustworthy car is proving to have many more benefits and teachable moments than we had anticipated.
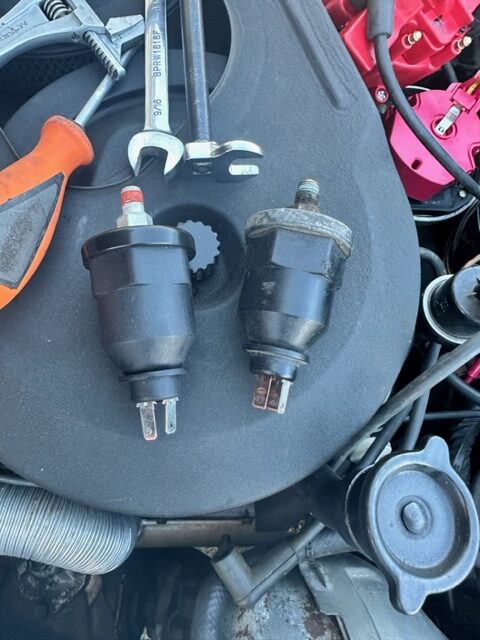
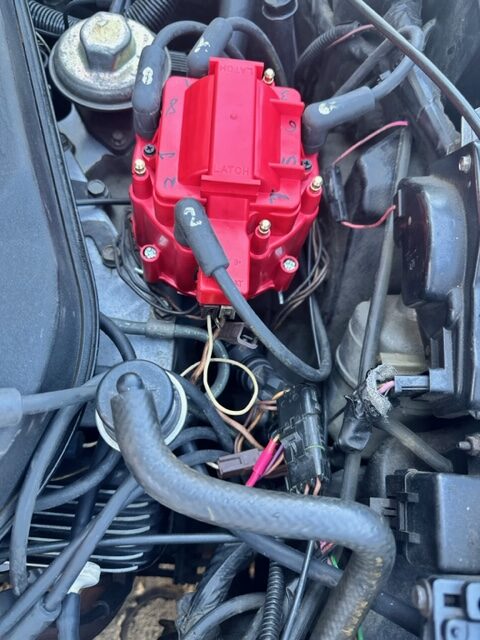




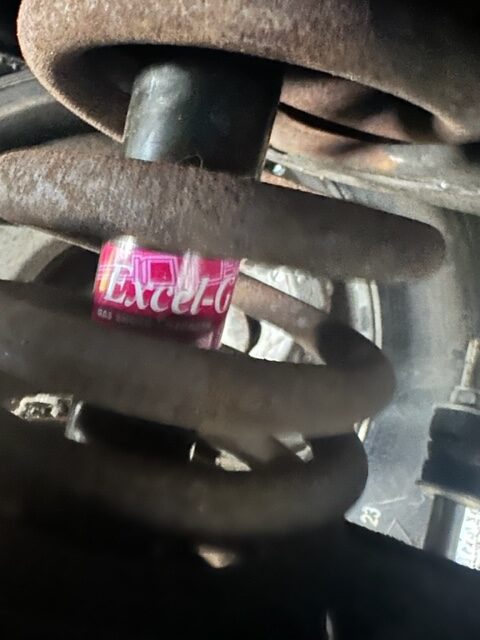

Fantastic story Keith, I enjoyed it very much! Cheers!
Thanks! Appreciate the feedback.
Keith, you are a great father and mentor. I loved the story. The 1982 Corvette is a fun car to drive and work on. Best wishes and many happy miles to Bradley.
Thanks. I’m blessed to have a young mag so engaged. I don’t take any of it for granted.
When working under the hood and disconnecting multiple hoses, connectors, etc, wrap a bright piece of painters masking tape around each component. This is a big help during reassembly.
> “drive, break, fix, drive, break again, fix again and repeat as necessary.”
Gawds, how I wish I had tools, a shop and a fleet of mentors as a teen.
That’s great! I wish I had that kind of tutoring when I was that age…
Wonderful story! So fabulous your son is interested in the analog world. The skills he is learning will pay dividends in the future.